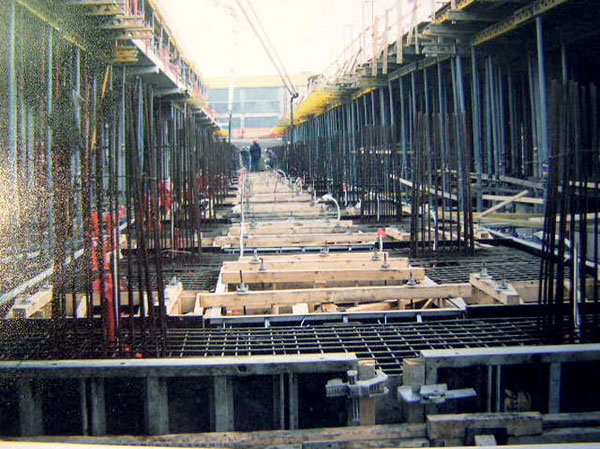
Technológia betonáže masívnych konštrukcií
Počas realizácie masívnych monolitických konštrukcií a v prvých mesiacoch po jej dokončení sa vyskytuje celý rad rizík, ktoré súvisia s procesom hydratácie a uvoľňovania veľkého množstva tepla. Problematika masívnych konštrukcií, vznik teplotných polí, sprievodných napätí a deformácií je síce už teoreticky zvládnutá, ale praktické riešenie jednotlivých stavieb je vždy špecifickým problémom.
![]() |
Poznáte výhody Klubu ASB? Stačí bezplatná registrácia a získate sektorové analýzy slovenského stavebníctva s rebríčkami firiem ⟶ |
V praxi sa totiž nepracuje s konštantnými, ale so stochastickými premennými hodnotami vstupných údajov (merné hydratačné teplo, teplota vonkajšieho prostredia a jednotlivých zložiek betónu, premenné fyzikálne vlastnosti zrejúceho betónu, presnosť dávkovania zložiek betónu a podobne). Rovnako aj požiadavky na výrobu, hustota výstuže, použitá mechanizácia, použitý materiál a iné okolnosti určujú vstupné parametre, ktoré sa zvyčajne veľmi líšia od teoreticky najvhodnejších. V technologickom predpise pre postup betonáže sa však musia stanoviť také opatrenia, ktoré povedú k realizácii kvalitnej konštrukcie aj za týchto nepriaznivých okolností.
Technologické opatrenia pre betonáž masívnych konštrukcií
Bežným technologickým postupom pri realizácii masívnych konštrukcií je ich pôdorysné rozloženie do blokov, ktoré sa betónujú po jednotlivých výškových stupňoch, pričom vertikálna pracovná škára nesmie byť priebežná. Je preto upravená schodnicovito a deliace steny sú z oceľových sietí. Jednotlivé výškové stupne sa betónujú po lamelách, pričom najdlhší interval medzi dokončením predchádzajúceho povrchu a ukladaním čerstvej betónovej zmesi (to znamená pri betónovaní dvoch nasledovných lamiel) je pre dodržanie monolitičnosti konštrukcie 8 až 10 hodín. Po vybetónovaní čiastočnej hrúbky nasleduje niekoľkodenná prestávka, ktorá umožní odvedenie vzniknutého hydratačného tepla. Týmto technologickým opatrením sa na prijateľnú hodnotu zmenšuje nebezpečný teplotný spád, ktorý podstatne ovplyvňuje deformácie zrejúceho betónu a je príčinou tvorby trhlín. Pracovné škáry treba navrhnúť vzhľadom na charakter namáhania konštrukcie, spôsob jej vystuženia, ako aj vlastnosti použitého čerstvého betónu.
Na niektoré masívne konštrukcia sa bežne v praxi kladie požiadavka na ich zhotovenie bez dilatačných a pracovných škár. V čase začatia tvrdnutia betónu treba zabezpečiť minimálny koeficient trenia o podklad, aby sa dosiahla eliminácia napätia od zmraštenia. Preto sa vytvára klzná medzivrstva. Samotná betonáž sa má realizovať od stredu konštrukcie na obidve strany súčasne, aby sa eliminovalo hydratačné zmraštenie a zabezpečili minimálne teplotné posuny. Pri takto navrhnutom technologickom postupe treba realizovať zvarenie výstuže do tuhého celku, aby nedošlo k posunutiu jednotlivých prútov pri pohybe betónovej zmesi. Čerstvý betón má mať nízku statickú viskozitu, ktorá zabezpečí malé rozliatie nevibrovaného čerstvého betónu, a tým vytvorenie clony pre vibráciu ponornými vibrátormi. Čerstvý betón sa takto vytláča smerom k obidvom čelám konštrukcie.
Pri realizácii masívnych monolitických konštrukcií treba voliť cementy s nízkym merným hydratačným teplom, používať prípravky na stekutenie čerstvého betónu a odďaľujúce začiatok jeho tuhnutia. Počet pracovných škár v konštrukcii by mal byť minimálny. Pred začiatkom betonáže je dôležitá dôkladná technologická a organizačná príprava vrátane dostatočných rezervných kapacít (je vhodné aj overenie navrhovaného technologického postupu v zmenšenom rozsahu). Po betonáži spodných vrstiev treba očistiť výstuž v hornej nezabetónovanej časti konštrukcie.
Konkrétny technologický postup betonáže základového bloku pod tlačiarenský stroj je jednoznačným dôkazom komplikovanosti a náročnosti realizácie tejto konštrukcie.
Opis konštrukčného riešenia základového bloku pod tlačiarenský rotačný stroj
Návrh technológie betonáže vychádzal z niekoľkých aspektov, ktoré sa predbežne overovali na pokusnom bloku a ktoré súviseli s možným vplyvom na výslednú kvalitu hlavného diela.
Špecifické aspekty projektu
Železobetónový blok so šírkou 5,5 m, hrúbkou 2,3 m a dĺžkou viac ako 96 m s objemom asi 1 050 m3 betónu bez dilatačných a zmrašťovacích škár predstavoval z hľadiska platných noriem odchýlku, predovšetkým pokiaľ ide o problém vzniku možných nekontrolovaných zmrašťovacích trhlín, ktoré by bez nevyhnutných technických opatrení rozdeľovali navrhnutý základový blok na staticky nevhodné dielce.
Aby sa splnila požiadavka na pevnosť betónu z hľadiska statického dimenzovania, projektant navrhol použiť betón triedy C 20/25.
Podľa rozboru chemického zloženia spodných vôd pendulárneho (nepriaznivého) charakteru išlo o vodu patriacu do kategórie sírano-vápenatých alebo sírano-horečnatých s vysokým agresívnym účinkom na železobetónové konštrukcie. Stupeň agresivity bol podľa ISO 9690 A 3 L, a teda podľa ČSN EN 206 – 1 (STN EN 206 – 1: 2002 (73 2403): Betón. Časť 1. Špecifikácia, vlastnosti, výroba a zhoda.) stupeň 5 c. Zo stavebného hľadiska to znamenalo realizovať viacnásobnú ochranu proti týmto agresívnym vodám. Táto ochrana spočívala v návrhu zloženia cementového betónu odolného proti tomuto typu agresívnych vôd a v návrhu účinného typu vonkajšej izolácie.
Na povrchu železobetónového základového bloku sa navrhli v projekte relatívne veľké priehlbiny pre technológiu rotačky, s pôdorysným rozmerom viac ako 4 m2, hlboké až 0,5 m.
Celý železobetónový blok sa musel uložiť na veľmi účinnú klznú medzivrstvu základovej škáry zloženú z dvoch vrstiev oddelených separačnou fóliou tak, aby sa na najnižšiu možnú mieru minimalizovalo trenie medzi podkladom a spodnou stranou bloku.
S celkovou koncepciou technického riešenia okrem statickej výstuže súvisela nevyhnutnosť realizácie obvodovej výstuže. Po obvode bloku na hrúbku 300 mm sa malo použiť 0,7 % výstuže v obidvoch na seba kolmých smeroch.
Po zmenšení hydratačného zmraštenia sa musel minimalizovať celkový obsah vody v čerstvom betóne na najnižšiu únosnú mieru, avšak s prihliadnutím na to, že doprava čerstvého betónu musela prebiehať čerpaním. Čerstvý betón v tomto prípade musel byť relatívne hustý, aby nedochádzalo k príliš rýchlemu rozlievaniu sa betónu v debnení, na druhej strane musel byť veľmi dobre spracovateľný ponornými vibrátormi.
Z technologického hľadiska išlo o čerstvý betón, s nízkou statickou viskozitou (rozliatie pri použití Haegermannovho kužeľa do 100 mm) a vysokou dynamickou viskozitou (VeBe maximálne V3°).
Vzhľadom na zložky kameniva v betóne a požiadavky na odolnosť a spracovateľnosť čerstvého betónu sa muselo použiť zvýšené množstvo cementu, čo pri nevhodnom vodnom súčiniteli mohlo vytvárať veľké zmrašťovanie s následným vznikom trhlín po ukončení hydratácie.
Táto skutočnosť sa pri návrhu betónu eliminovala voľbou triedy cementu CEM III/A 22,5, ktorý má relatívne vyšší obsah vysokopecnej trosky, ktorá spomaľuje začiatok aj koniec tuhnutia, pri zodpovedajúcom následnom náraste pevnosti, a rovnako nízky nárast počiatočného hydratačného tepla v priebehu zrenia. Súčasne sa použil systém účinných stekucovacích prísad retardujúcich začiatok tuhnutia cementu, aby tento proces nastal až po uložení čo najväčšieho množstva betónu. To však na druhej strane znamenalo vyššiu pevnosť, ako bola navrhovaná v projektovom riešení, čo sa pri úvodnom rokovaní s projektantom prediskutovalo.
Ďalej bolo potrebné, aby po vyvrcholení hydratačnej teploty v celom základovom bloku počiatočná pevnosť betónu predovšetkým v prostom ťahu bola taká vysoká, aby spoločne s daným vystužením prekonala vzniknuté napätia od teplotného zmrašťovania, ktoré súvisí s postupným ochladzovaním do prirodzeného stavu zrejúceho betónu.
Všetky tieto skutočnosti sa uviedli do základnej správy o technologickom riešení a pred začatím samotnej betonáže odskúšali na modelovom bloku.
Postup betonáže
Betonáž prebiehala od stredu základového bloku na obidve strany súčasne s tým, že čerstvý betón sa dodával súčasne dvoma čerpadlami na betón (obr. 1). Vzhľadom na statickú viskozitu čerstvého betónu sa betón dodával do čela postupovej hrany a až za touto „hrádzou“ sa spracovával ponornými vibrátormi na požadovanú objemovú hmotnosť, dopĺňal na predpísanú úroveň a povrchovo upravoval.
Obr. 1 Schéma postupu a spôsobu ukladania čerstvého betónu
Táto technológia ukladania čerstvého betónu umožnila zaplňovanie debnenia rovnomerne od stredovej časti postupne k okrajom. To malo hlavný význam pre postupnú hydratáciu a zároveň aj postupný vývoj hydratačného tepla v betónovom základovom bloku (obr. 2).
Zvláštny prípad tvorili odebnené priehlbiny na povrchu základového bloku ukotvené k výstuži, ktoré sa museli dokonale podbetónovať, bez toho aby došlo k ich zdvihnutiu, či dokonca vyplaveniu počas vibrovania betónu.
Retardovanie začiatku tuhnutia cementu v zmesi až na 19 hodín od pridania vody, spoločne so začiatočnou teplotou čerstvého betónu 10 °C a nízkou teplotou prostredia, ktorá bola iba 1 až 3 °C, bol tlak na základovú škáru postupný, zaťaženie hodnotou asi 5,43 ton na 1 m2 prebiehalo postupne s časovým oneskorením, takže deformácie celého bloku prebiehali ešte v plastickom stave betónu.
To umožnilo pri súbežnej kontrole nivelity dopĺňať výškový rozdiel medzi okamžitým dotlačením základovej škáry hmotnosťou čerstvého betónu a povrchom bloku ešte pred konečným vyrovnaním povrchu. Snaha o minimalizovanie vodného súčiniteľa a retardáciu začiatku tuhnutia sa prejavila relevantným značným nárastom hydratačnej teploty, ktorá si vyžiadala zvýšenú ochranu stien a povrchu oproti ochladzovaniu, aby teplotný gradient bol čo najnižší. Návrh betónu bol spracovaný tak, aby v okamihu keď hydratačná teplota zrejúceho betónu dosiahne vrchol a začne klesať, bol nárast pevnosti betónu postačujúci na podchytenie napätí v prostom ťahu vyvolávaných klesajúcou teplotou.
Zistené teploty a pevnosti betónu
Teplota betónu v železobetónovom bloku sa sledovala priebežne dvomi sondami v hĺbke 1 m vo vnútri bloku, dve merania prebiehali na povrchu a zároveň sa merala teplota vzduchu v mieste staveniska. Meranie prebiehalo v intervale 6 hodín od začiatku betonáže, až do 28. dňa, keď teploty dosiahli hodnoty blízke teplote prostredia. Začiatočná teplota ukladaného betónu bola v priemere 10 °C, po spracovaní narastalo hydratačné teplo až do vyvrcholenia, ktoré sa dosiahlo 4. deň po začatí betonáže a následne dochádzalo k pozvoľnému poklesu, ktorý prebiehal prakticky 28 dní.
Okrem teplôt sa sledoval aj nárast pevnosti v tlaku po troch dňoch 16,7 MPa, 17,0 MPa a 16,4 MPa a jej ďalší nárast pri klesajúcej vnútornej teplote betónového bloku. Po siedmich dňoch to už bolo 31,3 MPa, 31,1 MPa a 31,8 MPa. Priemerná pevnosť v tlaku po 28 dňoch bola 48,95 MPa.
Pre úplnosť sa realizovali skúšky betónu priečnym ťahom po 28 dňoch zrenia podľa ČSN 73 1318 (STN 73 1318: 1986: Stanovenie pevnosti betónu v ťahu) s hodnotami Rt, tr = 4 MPa, 43,4 MPa a 4,3 MPa, čo sú pomerne vyhovujúce hodnoty.
V kritickom čase kulminácie teplôt v bloku bola už pevnosť betónu na hodnote 60 % výslednej pevnosti, teda 29,37 MPa (obr. 3), čo je hodnota úplne postačujúca na udržanie celistvosti základového bloku, bez zmrašťovacích trhlín.
Obr. 3 Priebeh teplôt a pevností v základovom bloku (%)
K tejto skutočnosti prispela značnou mierou kvalitná realizácia klznej medzivrstvy, ktorá umožnila nízkym koeficientom trenia o podklad horizontálny posun v čase nárastu pevnosti pri poklese teplôt.
Záverečné zhrnutie
Pokles spôsobený dotlačovaním zeminy v základovej škáre v priebehu betonáže hodnotou 5,43 t/m2 sa eliminoval priebežným dopĺňaním a vibračným zhutňovaním betónu pred vyrovnávaním povrchu za priebežnej kontroly nivelity.
Vzhľadom na relatívne nízky obsah vody v betóne (vodný súčiniteľ w < 0,38) bolo vertikálne zmraštenie na výšku 2,3 m menšie ako 3 mm. Avšak dotláčanie na základovú škáru bude prebiehať dlhší čas, čo však súvisí s dlhodobou stabilitou základovej zeminy a nie so zmrašťovaním betónu. Celkové zníženie povrchu bloku vplyvom zmraštenia, tak aj vplyvom dotlačenia základovej škáry pred montážou rotačky by nemalo prekročiť v súčte hodnotu 5 mm. Túto hodnotu možno vo vzťahu k hmotnosti základového bloku považovať za konečnú. Navrhnutá technológia betonáže s daným zložením betónu sa ukázala ako správna v plnom rozsahu. Príspevok vznikol s podporou výskumného zámeru MSM6840770006 Manažment udržateľného rozvoja životného cyklu stavieb, stavebných podnikov a územia.
TEXT: Josef Doležal a Pavel Svoboda
FOTO: archív autora
Doc. Ing. Pavel Svoboda, CSc., pôsobí na Katedre technológie stavieb Stavebnej fakulty ČVUT v Prahe.
Recenzoval doc. Ing. Ivan Juríček, PhD., ktorý pracuje na Katedre technológie stavieb Stavebnej fakulty STU v Bratislave.
Literatúra:
1. Doležal J.: Záverečná správa o skúškach betónovacích strojov a zariadení na betonáž vozoviek. Praha: Vojenské Stavby, 1996.
2. Doležal J.: Stavby cementobetónových vozoviek. In: Stavitel, 1998, č. 5.
3. Doležal J., Svoboda P.: Priemyselné podlahy a komunikácie v priemyselných parkoch. Bratislava: JAGA, 2009.
4. Škvára F.: Štúdia reaktivity portlandského slinku. Praha: ČSAV a VŠCHT 1983.
Článok bol uverejnený v časopise Stavebné materiály.